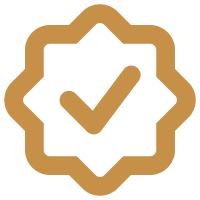
More precise detection of wafer/chip defects
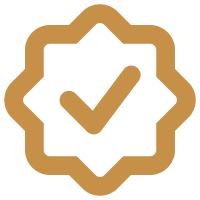
Automated classification of defect types
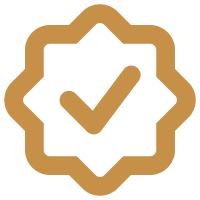
Stronger pattern defect detection capabilities
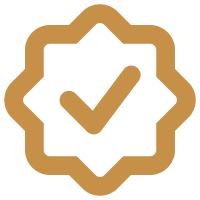
Significantly improved detection efficiency
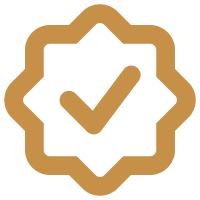
Reduced human intervention and subjective errors
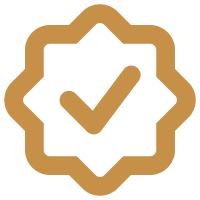
Enhancing defect detection for light guide plates and diffusion boards
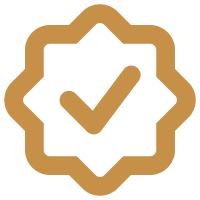
Accurate detection of fine circuit pattern defects
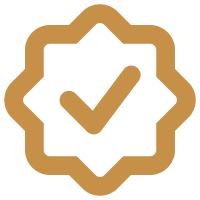
Improved detection rate for color filter and CF defects
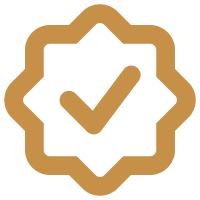
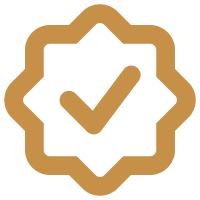
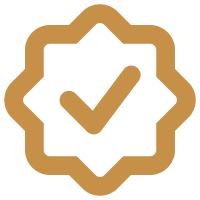
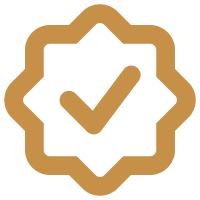
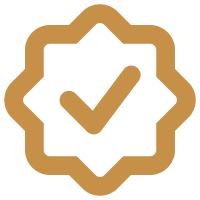
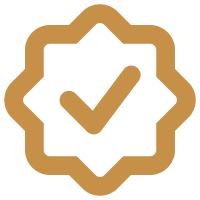
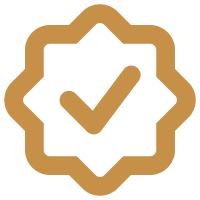
Enhancing defect detection for complex metal/mechanical components
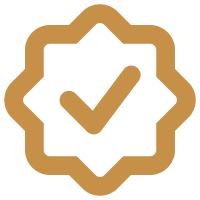
Handling diverse metal materials and surface characteristics
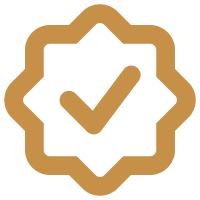
Improving defect detection for critical functional components
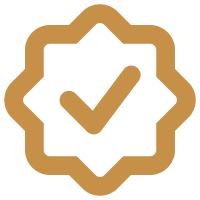
Shortening programming time for complex product inspections
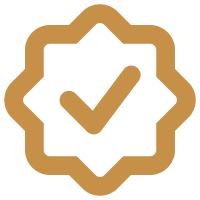
Enhancing high-speed production line inspection adaptability
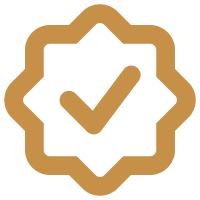
Real-time problem identification and resolution
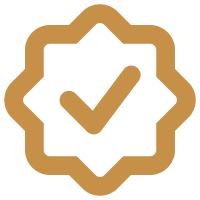
Reducing human errors
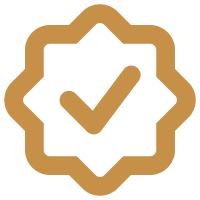
Reducing customer complaints and increasing ROI
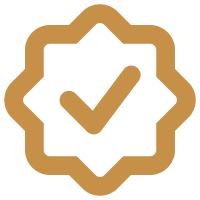
Lowering production costs
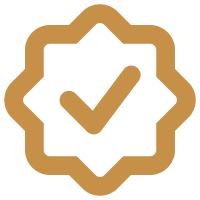
More precise detection of food surface defects
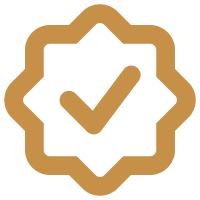
Accurate identification of foreign objects within food
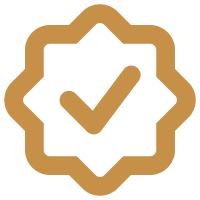
Automated food shape recognition and grading
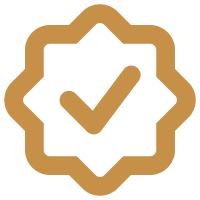
Rapid inspection of food packaging integrity
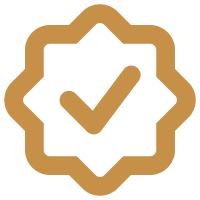
Improved detection of subtle surface defects on medical devices
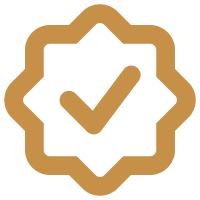
Accurate inspection of medical packaging integrity
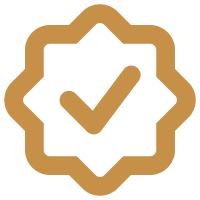
Realization of medical label character recognition
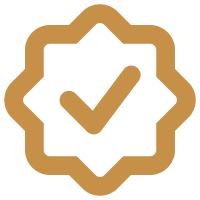
Improved inspection efficiency and reduced human risks
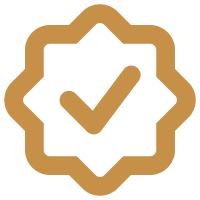
Improved detection accuracy
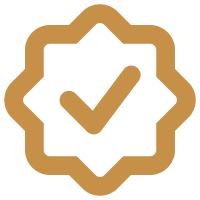
Flexible defect definition and classification
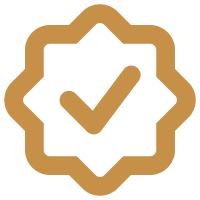
Highly adaptive optimization of inspection
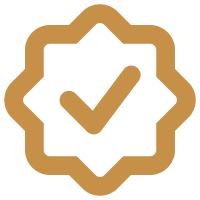
Automated, unattended operation
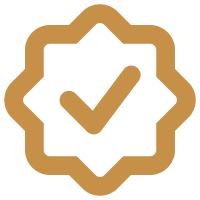
Improved detection of small defects on printed products
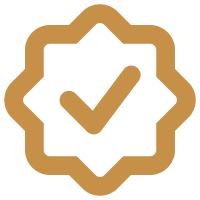
Accurate text/code recognition Labels/printed products often feature text, barcodes, and other encoded information.
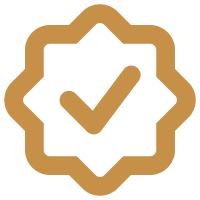
Efficient inspection of complex patterns and image defects
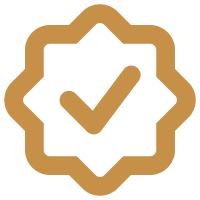
Significantly improved inspection efficiency
Textiles/Plastics
Solutions:
At present, most yarn factories still rely on manual inspection, which has a high missed detection rate and consumes a long time. There are many types of yarn defects, such as paper tube stains, deformation, dirty yarn, broken yarn, thrown yarn, fluff, and two-color yarn. Manual inspection is not conducive to actual quality requirements, and automatic optical inspection (AOI) is also difficult to detect when facing non-fixed defects, and the false detection rate is high, and manual re-inspection is still required. In order to allocate labor costs to more efficient work, yarn inspection should seek higher efficiency inspection solutions.Using SolVision's Segmentation technology, feature extraction is performed on various defects on paper tubes and yarns, and AI model training is performed to enable AI to learn to identify defect features and quickly and accurately find various defects. It can effectively improve the detection rate, finished product yield and reduce the quality inspection burden. With the increase in the number of learning samples, the ability of AI to identify defects can be continuously optimized, and the learning results can also be quickly introduced into various production lines.
- High-speed inspection with a maximum inspection capacity of 60PCS/second (2M).
- AI deep learning identifies defects.
- Simultaneous inspection quantity can detect up to 10 areas at the same time.
- Inspection area 2mm2-200mm2.
- The inspection camera uses a 2M-25M high-speed area camera.
- The inspection accuracy camera is equipped with a lens resolution of 0.001mm-0.05mm.
- Measurement capability can detect 2M 60 frames/second or 5M 4 frames/second per second.
- Detailed measurement data classification is stored in different directory folders according to camera sequence, by date and order. Automatically create file names based on date and time.
- NG photo processing automatically generates directory folders and automatically creates file names based on date and time. During the inspection, click on the NG thumbnail or tile in the screen, and the complete photo can be popped up.
- Real-time measurement trend chart can display the data of the last 1000 points of each axis.
- The operation mode has operation mode (only display data), engineering mode (including real-time images) and commissioning mode.
Socks have a variety of defect forms, including snags, wrinkles, and tears. The shape, size and position of these defects are not fixed. Traditional AOI is suitable for the inspection of whole pieces of cloth, but it has difficulty in detecting defects that are not fixed, and it is easy to make false detections. Therefore, manual re-inspection is still required.By collecting images of sock defects such as snags and wrinkles, and using SolVision's Segmentation technology to complete the training of the AI model, it is possible to quickly and accurately find defects, classify different defects and remove defective products. This can help to control product quality and improve production efficiency. By classifying and analyzing defects, it is also possible to optimize the overall manufacturing process.
Semi-automatic inspection equipment, fully automatic discharge, high-speed and high-precision detection, precise defect marking, authority management, size confirmation, appearance inspection, intelligent inspection data statistics, non-conforming product analysis, report output, support for remote calibration management
Engineers can use the Cognex Deep Learning defect detection tool in unsupervised mode to train the software on a set of "good" airbag images to create a reference model of the airbag. All features that deviate from the normal appearance of the model will be depicted as anomalies. In this way, Cognex Deep Learning can reliably and consistently detect all anomalies, such as pinholes, cracks, holes and unusual stitching patterns. It quickly identifies and reports areas of fabric defects, completely eliminating the need for expensive defect databases.
- High-speed inspection with an inspection capacity of 30 meters/minute.
- Maximum inspection width 360mm.
- Maximum roll diameter 450mm.
- High-resolution line scan camera uses color 8K and black and white 16K.
- Learning function has AI artificial intelligence function to learn to identify OK/NG products, and then inspect defects.
- Inspection capability can detect defects of 0.12mm2 for color and 0.06mm2 for black and white.
- Defect threshold can set the defect length and width threshold, and all above the threshold can be detected.
- Defect marking has defect marking capability, and you can choose to use a brush or laser marking.
- Management function has management level, engineer and operator level, and can set operation permissions.
- Real-time display has real-time display of scan image thumbnails and full images.
- Automatic recording can record the number of defects, and the statistics table and curve chart are displayed on the screen.
- Defect photos can be selected whether to save the defect photos.
RGI Double-Sided Series uses conveyor belt flipping or double glass disc inspection to simultaneously inspect double-sided defects, but defects may not be screened out due to refraction or dirt through the glass.
- High-speed inspection with a maximum inspection capacity of 1000PCS/minute.
- Inspection turntable diameter 250mm-700mm.
- Standard machine size 850mm×width 850mm×height 1800mm.
- High-resolution area camera uses 1.3M-25M.
- Learning function has AI automatic learning function to identify OK products and then check NG defective products.
- Inspection capability can detect defects of 0.01mm2 for color and 0.005mm2 for black and white.
- Defect threshold can set the defect length and width threshold, and all above the threshold can be detected.
- Defect marking has defect marking capability, and the selector can be used to separate the materials into OK/NG/NULL three hoppers.
- Management function has management level, engineer and operator level, and can set operation permissions.
- Real-time display has real-time display of inspection thumbnails and full images.
- Automatic recording can record the number of defects, and the statistics table and curve chart are displayed on the screen.
- Defect photos can be selected whether to save the defect photos.
The colorful nature of ribbons makes automatic optical inspection difficult. Due to the complex fabric patterns, it is difficult to find specific feature points. Automatic optical inspection (AOI) is prone to missed detection or misjudgment of defects due to changes in patterns and colors.Using the Segmentation technology in SolVision to detect ribbons of various colors and patterns can accurately find the location, size and shape of defects such as holes and loose threads. Both the detection speed and accuracy can meet the standards. By recording and analyzing the appearance of defects, it is possible to trace back the problems in the manufacturing process and improve the product process.
- Common appearance defect inspection of textile fabrics: broken warp, hairiness, color difference, dirt, white spots, creases, indentations, damage, etc.
- Inspectable fabrics: plain weave, knitted fabric, glass fiber fabric, non-woven fabric, bonded fabric and brushed fabric
When using traditional automatic optical inspection to detect plastic defects, it is difficult to quantify the defects due to the variety and changing positions of the defects. It is easy to encounter the problem of insufficient defect samples, which makes it difficult to quantify the defects. This leads to insufficient detection accuracy. If manual inspection is maintained, the detection speed is relatively slow and the quality is inconsistent. There are still many difficulties in identification.By using SolVision's Segmentation technology, a defect database is established for the shape and color of rubber product defects, and then AI is used to learn the characteristics of the defects. This can identify defects of various types and positions. With the increase of learning images, the ability of AI visual inspection is continuously optimized, which significantly improves the accuracy of rubber defect identification and effectively solves the problem of unstable detection of rubber product defects.
In the production of fasteners, the most common injection molding defects are mold release agent oil stains, white spots, burrs and debris, of which oil stains are the most difficult to detect. White spots, burrs and debris have obvious features in the image, while products with oil stains are very similar in appearance to general good products, which are difficult to detect.Using the Segmentation and Classification technology of Solomon SolVision AI image platform, deep learning is performed for each type of surface defect. After the AI model is trained, it can immediately detect all types of defects including oil stains.
In addition to judging whether the packaging is sealed, in order to find the root cause of the problem, it is necessary to further confirm the type and cause of the incomplete seal. However, because the different types of sealing defects are very different, and the surface of the object is highly reflective, it is not easy to find and classify the defects with either the naked eye or automatic optical inspection (AOI).Combining machine vision and artificial intelligence, Solomon uses the Classification tool of SolVision to define the state of good seal from the image and compare it with multiple defects, including incomplete bottom seal, no seal on both bottom and side, and incomplete seal on both bottom and side. It can instantly detect incompletely sealed packages and classify the defects.
NGI Glass Disc Series is a series of glass disc inspection machines that use the light transmission properties of glass to automatically detect defects on both the top and bottom of the glass disc.
NCI Conveyor Belt Series is an entry-level automatic inspection machine that is ideal for budget-conscious buyers who need to inspect products for single-sided defects.
Matrox DA4.0 software uses a flowchart-based user interface, allowing users to easily perform bottle inspection tasks through the built-in software development kit (SDK), including liquid level detection, cap, safety ring, and label height detection.
- Full color/multi-spectral scanning (RGB CCD sensor), wide range of defect detection
- Multiple flash exposure technology, can simultaneously detect defects under different light sources
- Module linearity calibration (CCD), can effectively detect wide range of color difference defects
- Defect stitching is available to inspect large-sized defects
- Integrated encoder, can output defect map
- High-speed inspection with a maximum inspection capacity of 1PCS/second (2M)
- AI deep learning identifies defects.
- Adjustable inspection track.
- Inspection area 2mm2 -200mm2.
- The inspection camera uses a 2M-25M high-speed area camera.
- The inspection accuracy camera is equipped with a lens resolution of 0.001mm-0.05mm.
- Measurement capability can detect 2M 60 frames/second or 5M 4 frames/second per second.
- Detailed measurement data classification is stored in different directory folders according to camera sequence, by date and order. Automatically create file names based on date and time.
- NG photo processing automatically generates directory folders and automatically creates file names based on date and time. During the inspection, click on the NG thumbnail or tile in the screen, and the complete photo can be popped up.
- Real-time measurement trend chart can display the data of the last 1000 points of each axis.
- The operation mode has operation mode (only display data), engineering mode (including real-time images) and commissioning mode.
- Built-in special lens and light source
- Full Chinese operation interface
- Quick adjustment page for product fine-tuning
- Statistical functions (total inspected/qualified/defective quantities)
- Defective image storage and classification
- Ability to adjust settings during inspection
- Complete rejection mechanism planning (low/medium/high speed, contact/non-contact type)
- The equipment can handle up to 1000pcs/minute at the fastest
- Fully Chinese one-to-many operation interface
- One-to-many screen micro-adjustment quick page
- Independent statistical functions for each screen (total inspected/qualified/defective quantities)
- Independent defective image storage and classification for each screen
- Ability to adjust settings during inspection
- Complete rejection mechanism planning (low/medium/high speed, contact/non-contact type)
- Equipment can process up to 800 pcs/minute at maximum speed
- Separate independent mechanisms for each station
Fully automatic inspection equipment, fully automatic loading and unloading, high-speed and high-precision inspection, precise defect marking, real-time yield statistics chart, authority management, size confirmation, appearance inspection, intelligent inspection data statistics, defect analysis, report output, support remote calibration management
The system can detect defects such as line defects, area defects, foreign objects, scratches, and blisters. It also provides intelligent inspection data statistics, non-conforming product analysis, report output, and support for remote calibration management.
Combining the AI Image Recognition Platform AIWinOps delivers intelligent manufacturing solutions, applying AI + AOI techniques to industries such as petrochemicals, golf club manufacturing, semiconductors, mechanical part fabrication, and textiles.